History of Rockford Toolcraft Incorporated
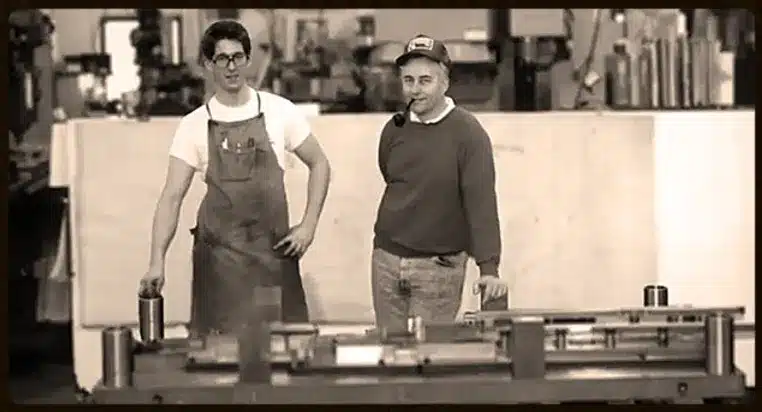
1976 – Rockford Toolcraft opens on March 12 at 2323 23rd Avenue in Rockford, Illinois. Design and build Tool & Die job shop, 500 sq. ft.
Jerry Busse & Terry Wilson Co-Owners. (2 employees)
1977 – Hired first employees and first Tool & Die apprentice (5 employees)
1978 – Moved to a larger facility at 2101 23rd Avenue in Rockford, Illinois. 4000 sq. ft. (8 employees)
1979 – Bought first CNC Wire EDM in a Rockford Tool & Die shop. (12 employees)
1980 – (13 employees)
1981 – Added second CNC Wire EDM. (15 employees)
1982 – Added large bed 250-ton tryout press (20 employees)
1983 – Begin planning construction of new plant and Stamping Division. (22 employees)
1984 – Broke ground on new plant. (23 employees)
1985 – Built and moved to a new 21,000 sq. ft., air conditioned plant. Started Stamping Division with three presses. (25 employees)
1986 – First plant addition; added large bed 600-ton press.
Terry Wilson sells out, Jerry Busse becomes 100% owner. (30 employees)
1987 – Added first CNC milling machine and CAM software. (36 employees)
1988 – Second plant addition; added large bed 500-ton press. (35 employees)
1989 – Installed CAD Design System and added large CNC Machining Center. (38 employees)
1990 – Third plant addition. Added third C.N.C. Wire E.D.M. (40 employees)
1991 – Fourth plant addition; added 400-ton press. (44 employees)
1992 – Fifth plant addition; added 300-ton press line. (50 employees)
1993 – Sixth plant addition; added second CNC Machining Center.
Tom Busse is promoted to Vice President. (60 employees)
1994 – Seventh plant addition; added new 150-ton press line. (65 employees)
1995 – Added fourth CNC Wire EDM. (75 employees)
1996 – Eighth plant addition; added new 1000-ton press line. (88 employees)
1997 – Ninth plant addition; added 300-ton and 600-ton press lines. (100 employees)
1998 – Tenth plant addition; added four new CNC Machining Centers. (115 employees)
1999 – Added 1500-ton press line. (120 employees)
2000 – Eleventh plant addition, 126,000 sq. ft. total; added two new press lines (150 and 300-ton). Leased 25,000 sq. ft. warehouse nearby and purchased 50,000 sq. ft. adjacent plant, on three acres of land, for future expansion. (130 employees)
2001 – Built 40,000 sq. ft. “Plant 2” on 13 acres. Added new 1000-ton press line @ plant 1 and a Robotic Weld cell @ plant 2. (135 employees)
2002 – Added five new large stamping press lines, new laser machine, and press brake and shear. (145 employees)
2003 – Built 40,000 sq. ft. addition to Plant 2. Added three 800 ton presses, a tool room and moved all secondary operations to plant 2. (165 employees)
2004 – Started a second 40,000 sq. ft addition at Plant 2. Ordered new 1000 ton Minster “HeviBlanker” press line. Added fifth CNC Wire EDM to plant 1. (190 employees)
2005 – Completed 40,000 sq. ft. addition at plant 2 (120,000 sq. ft. total) and added four press lines to Plant 2. Added massive coil line to 1500-ton press at Plant 1 with .500” x 36” @120,000ksi straightening capabilities. (205 employees)
2006 – Completed 30,000 sq. ft. addition at Plant 2 (150,000 sq. ft. total). Added 4400 ton transfer press line and a “Super-massive” coil line at Plant 2. Added Heat Flattening Department at Plant 2. (215 employees)
2007 – Added 3000 sq. ft. office expansion with large training facility at Plant 1. Added a Fanuc Robot to load large stampings in and out of 800 ton press at Plant 2. (225 employees)
2008 – Added a second robotic welding cell, a complete parts washing system and a new 6kw LASER system. (240 Employees)
2009 – Added new “Arku Flatmaster” precision parts leveler. Maintained employment of 240 people in a difficult business year. (240 Employees)
2010 – Added (3) 600 ton presses, new robotic welder, new wire E.D.M. and a new CNC Machining Center. (250 employees)
2011 – Added 41,000 sq.ft. addition to plant 2, a 4kw Amada Laser with full automation, an Amada Fabvision scanner, an 800 ton Minster press, a Genesis dual head robotic welder and 2 Romer portable 3D scanners. Tom Busse is promoted to President, Jerry Busse semi-retires. (300 employees)
2012 – Added Amada “Theta” 5 Axis Laser, (3) 500 ton “Verson” presses, (1) Extra Heavy Duty “Minster” Straightener, Installed (24 total) “Big Ass” Fans in both plants. Tom Busse becomes part owner of the business. (350 Employees)
2013 – Expanded into 48,000 sq ft building connected to plant 1, moved 8 presses into it from plant 2. Added (2) 1500 Danly presses (132” x 84”) with .500 x 60” “FeedLease” feed lines at plant 2. New “Cut 400” Charmilles Wire EDM, new Hurco VMX-50 machining center, added an Ingersoll Rand Material lift system to plant two. Bought new 2014 Freightliner “Cascadia” class 8 truck. (360 employees)
2014 – Added new 20 ton crane, Hurco “VMX 40” Machining Center, (3) Feed lease Feed lines, “Cut 300″ Charmilles Wire EDM, Okamoto Grinders (2) 6″x18″ & (1) 20″x48”, Amada 4000 Watt Fiber Laser w/6 Pallet Automation. (370 employees)
2015 – Added 2nd Amada “Theta” 5 Axis Laser and a Gigabot 3.0 3D Printer (23″x30″x23″). (350 employees)
2016 – Added 5 Bridgeport Milling Machines, 3 Drill Presses & updated Dust Collection System. (325 employees)
2017 – Added Automotive Welding Cell, Press Monitoring Technology, Oil Recycling System and a 25/35 Versa Lift (375 employees)
2018 – Added 5th Robotic Welder, Alliance 4 Stage Parts Washer, “Cut 350” Charmilles Wire EDM & Kalmar Ottawa “Yard Truck”. (410 employees)
2019 – Added new Oil Recycling equipment, rebuilt both clutches on 4400 ton “Brutus” press, added new ERP system Plex: going live February 2020 (380 employees)
2020 – Implemented “Plex” ERP system, continued steady operations during COVID-19 pandemic without laying off any employees. We SURVIVED!! Looking forward to 2021!! (350 Employees)
2021 – Added Trumpf “8030” 5 axis Fiber Laser, 2021 Freightliner “Cascadia” Class 8 truck, (3) Okamoto 12”x24” Surface Grinders (380 employees)
2022 – Added new Genesis Robotic Weld Cell, “Cut P 550” Charmilles Wire EDM, 2022 Freightliner M2 Box Truck (400 Employees)
2023 – Added new “Hurco” VMS 50i Machining Center, 300 Gallon Oil Recycler, 200 hp Air Compressor, 20 ton Bridge Crane.
Jerry Busse sells his share of the business & buildings/real estate.
Tom Busse becomes 100% owner. (400 employees)
2024 – Added 33,000 sq ft addition to Plant 2, Okuma MCVAII Bridge Mill, Okamoto 6 x 18 surface grinder, 600-ton Minster press control upgrade. (365 employees)
To be continued…